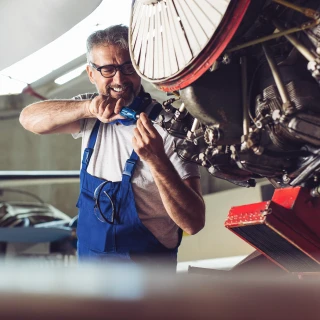
Smart maintenance: from fail and fix to prevent and predict
In today’s highly competitive market, you must deliver high-quality products quickly and cost-effectively. Downtime is a disaster, as is malfunctioning machinery or equipment that hampers product quality. Hence, the importance of superior maintenance. Driven by innovations like big data applications, the Internet of Things, machine learning, augmented reality, etc., maintenance is becoming increasingly smart.
Smart maintenance is about leveraging new technology such as mobile solutions, big data applications and IoT, to ensure that all the equipment required for production operates at 100% efficiency at all times.